Tung Ho Steel's Business Strategy
New Rolling Mills to be Constructed in Taiwan and Abroad
Mr. Ho, Tung Ho Steel
Chairman and President
Mr. Huang,
President of Tung Ho Steel Vietnam
Second Rolling Mill to be Constructed
Expansion to Vietnam
Meeting Demand with Variety
Countermeasures Against Imported Materials from China
Tung Ho Steel, a leading Taiwanese electric furnace steel manufacturer, acquired 100% ownership of Fuco Steel Corporation (renamed Tung Ho Steel Vietnam) in Ba Ria-Vung Tau Province in Vietnam in October 2015, and began factory management in full swing in January of this year. While their Vietnam site has only produced steel up to this point, the company began construction of a new rolling mill that is expected to commence production at the end of August of next year. In this interview, we asked Henry Chieh-Teng Ho, Chairman and President of Tung Ho Steel, and Huang Bing Hua, President of Tung Ho Steel Vietnam, for their views on the current situation and future policies in Vietnam.
―The second rolling mill will be constructed in the Taoyuan factory in Taiwan.
Henry Chieh-Teng Ho, Chairman and President of Tung Ho Steel ('Ho' hereinafter): The Tung Ho Steel Taoyuan factory does not have a furnace and produces all products by direct rolling. Thus, we always have the capacity for extra steel production, in the event that problems occur during rolling. The Taoyuan factory produces 1.5 million tons of steel per year, which is far larger than the rolling production capacity in the first rolling factory, namely 750-800 thousand tons per year. This should balance the steel production and rolling capabilities once the second rolling mill commences.
Huang Bing Hua, President of Tung Ho Steel Vietnam ('Huang' hereinafter): Another reason why we have decided to construct the second rolling mill is that six years have passed since the first rolling factory was constructed in 2010, and we see that the production with direct rolling has been successful. We will cut production costs by establishing two direct rolling line production systems and will not only be a domestic competitor within Taiwan, but we will work against the importation of materials from China.
Ho: In Taiwan, where energy costs are expensive, the impact of direct rolling is significant. We believe that it can generate a cost difference of approximately 15-25 dollars, compared to that of single-rolling manufacturers in Taiwan, which purchase billets from China and use furnaces to produce their final product.
―Why Vietnam?
Ho: One reason is that we can expect that the demand for steel will rise in Vietnam. Another reason is that the demand for steel in Taiwan has not risen, the market has been shrinking, and engineers in their 40's and 50's are losing their jobs. I want them to try this new challenge in Vietnam. On top of everything, young Taiwanese people do not want to work in factories nor do they respect skilled engineers. On the other hand, young Vietnamese people want to learn skills from these people as much as they can and treat them as their 'masters.' This should make engineers proud.
―You will produce a variety of products in Vietnam. Why?
Huang: In Vietnam, manufacturers that supply more than deformed bars already exist. If we only offer deformed bars, we cannot meet the various demands of the steel distributors. Ho: The final products may be different, but we, Tung Ho Steel and Tung Ho Steel Vietnam, consider them all as steel products for construction. Also, please note that we do not produce shaped steel in Taiwan.
―What will the production system look like in Vietnam?
Ho: We will construct a rolling mill with a production capacity of 600,000 tons per year in Vietnam. It will not have a furnace, but will produce products, including deformed bars, wire rods, small equal angle steel products, and channel shaped steel products, all by direct rolling.
Huang: Shaped steel production requires more energy for the furnaces than deformed bars, so we can enjoy even more effects from the cost reductions. We will control the speed, etc., of continuous casting in five strands, enabling them all to direct roll. Also, it is important to conduct highly accurate production in both the electric furnaces and during out-pile refining (LF). Another reason that we did not put a furnace in is that we not only care about costs but also about the environment. We want to introduce an environmentally friendly factory model, like the Taoyuan factory, to Vietnam.
(Daigo Hayama, Ho Chi Minh)

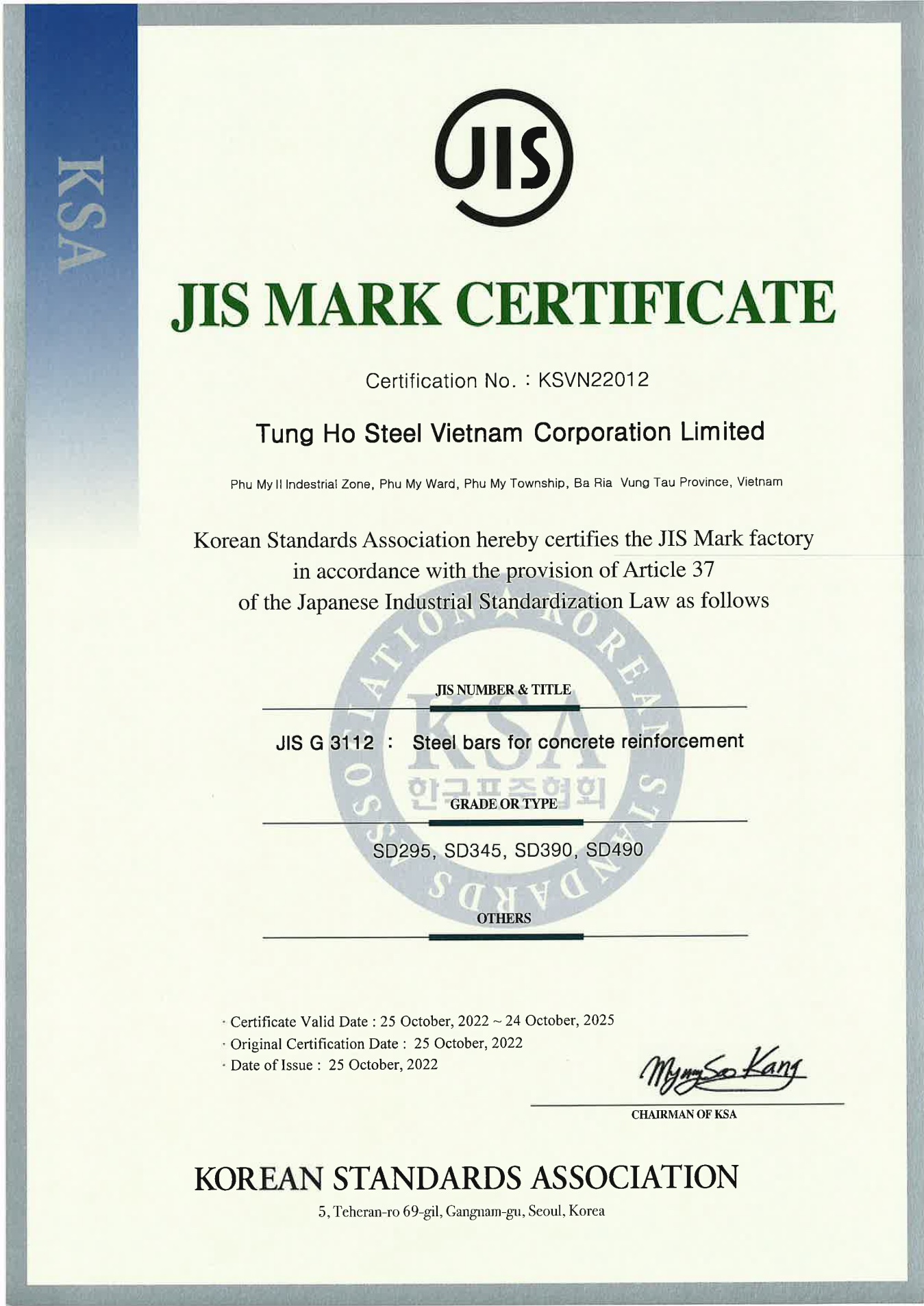
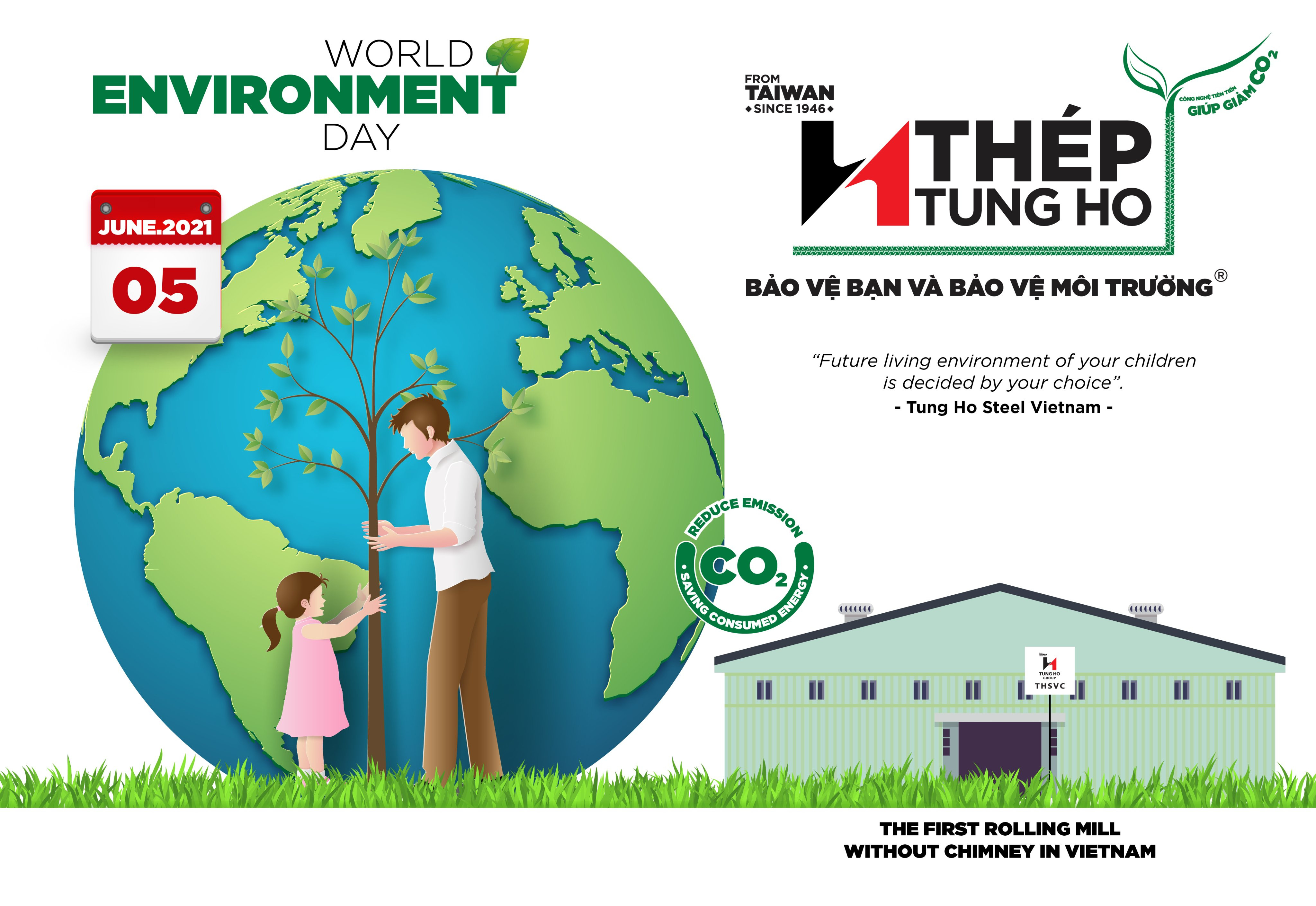
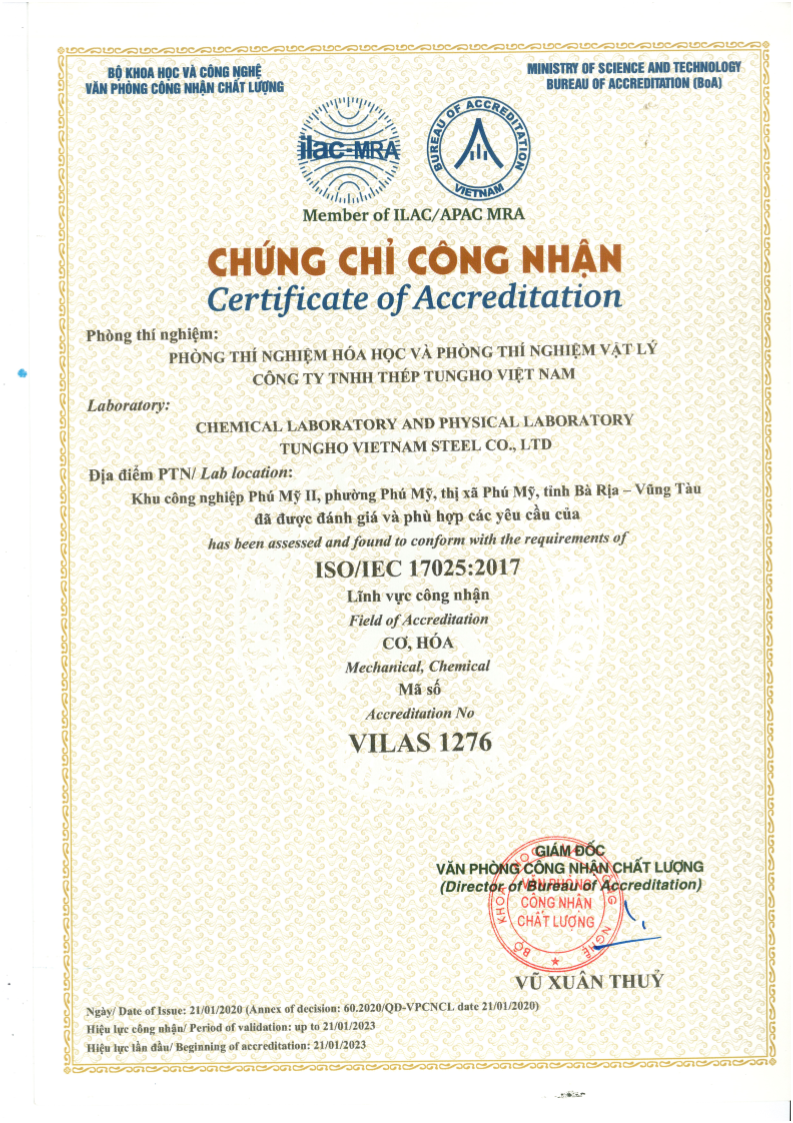
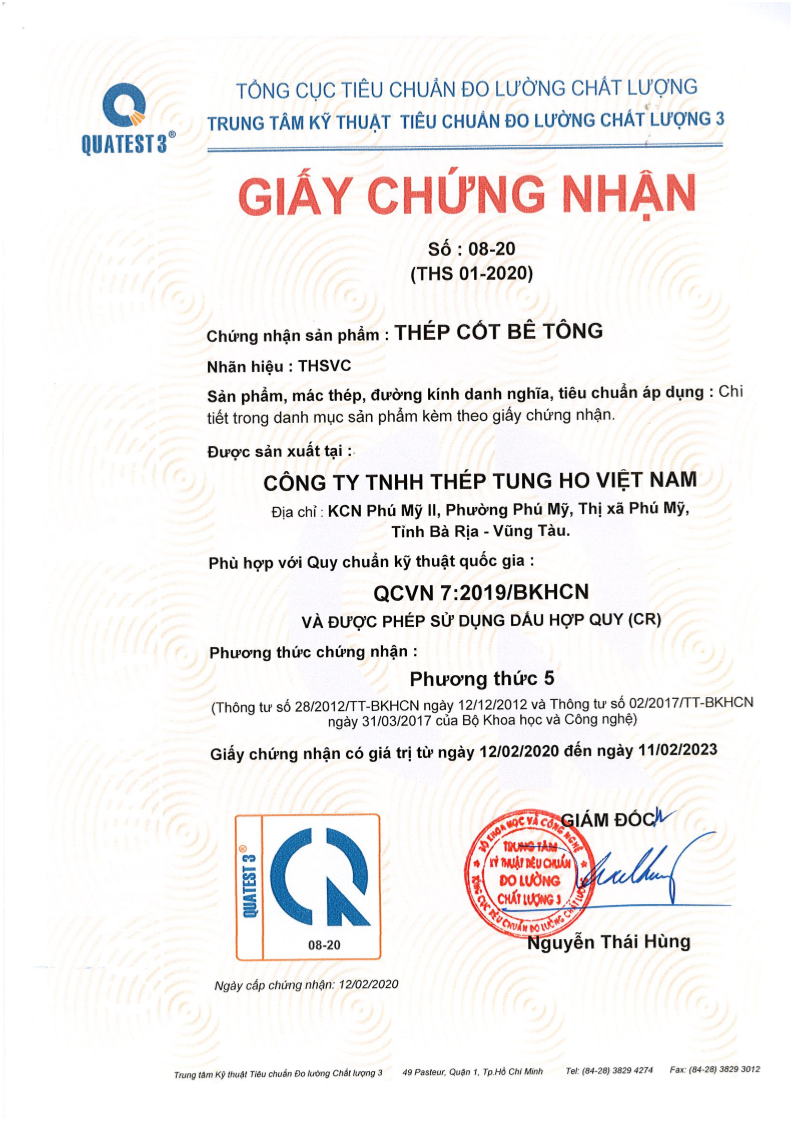
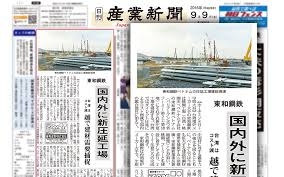
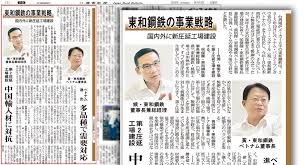
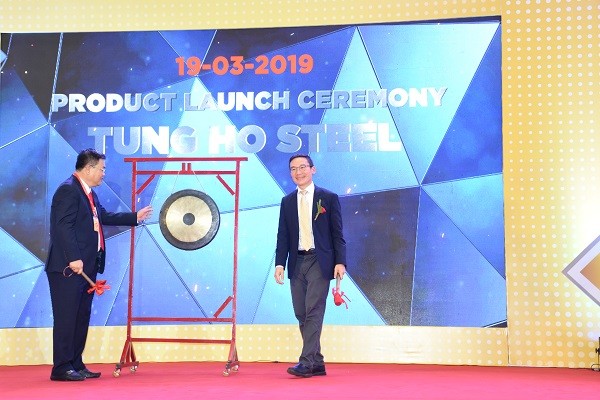